What are the key principles of Material Requirements Planning ?
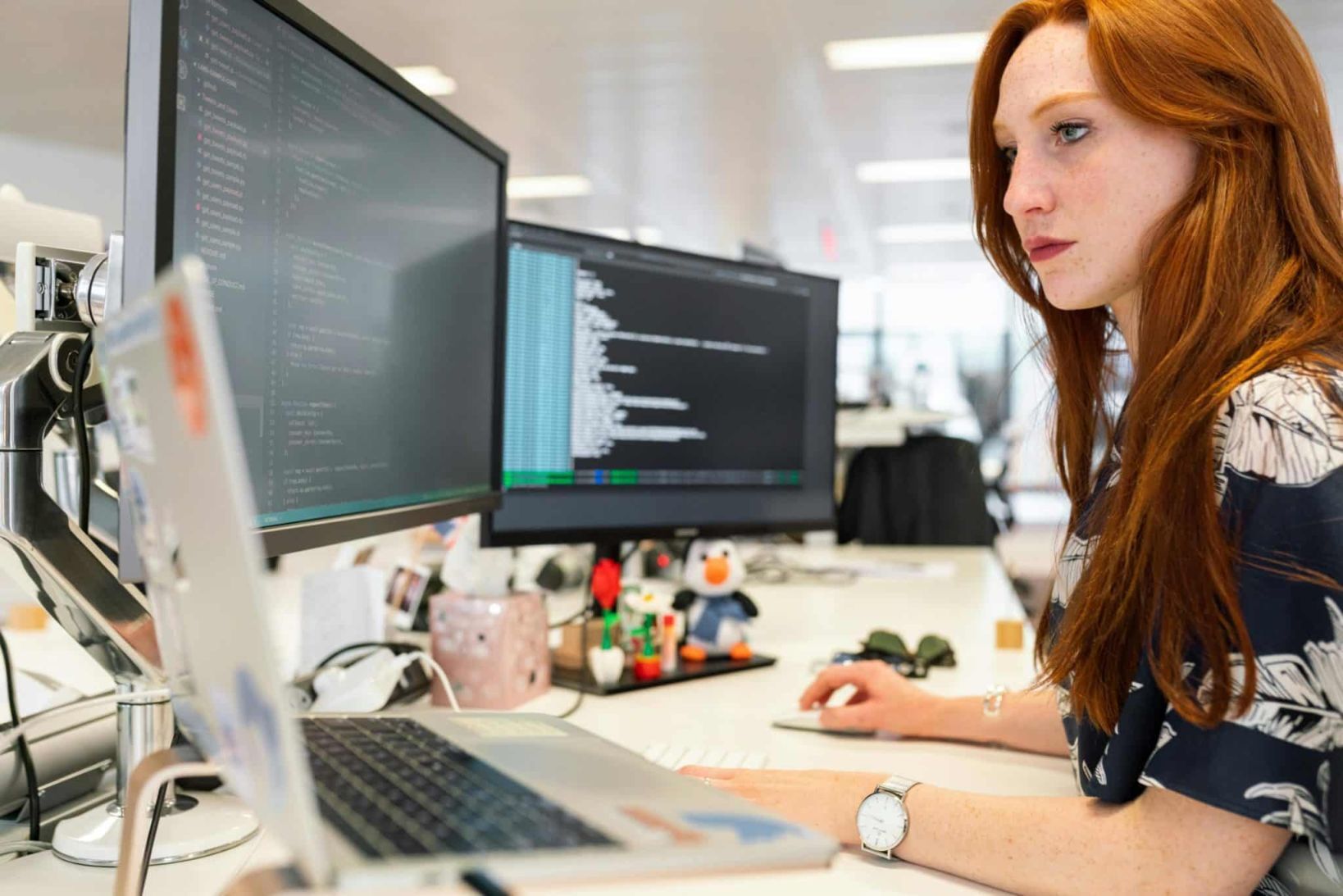
What is Material Requirements Planning?
Material Requirements Planning (MRP) is a planning and control system utilized primarily in manufacturing operations to manage inventory levels, schedule production, and coordinate supply chain activities. The main goal of material requirements planning is to keep inventory levels low while ensuring that materials and components are available when needed in the production process to meet customer demand. The MRP process involves a series of structured steps to determine customer demand, allocate resources, and schedule production, integrating various business functions to optimize material management.
MRP is based on three essential pieces of information: the master production schedule, the bill of materials, and the inventory status file. By integrating these data sources, the MRP system helps manufacturing companies control inventory, schedule production activities, and improve overall manufacturing efficiency.
What is MRP?
Material Requirements Planning (MRP) is a software-based integrated inventory and supply management system designed for businesses. It serves as a planning and control system for inventory, production, and scheduling, helping companies manage their production inventory levels and supply chain more effectively. MRP systems facilitate production planning by ensuring that the right materials and components are available when needed in the production process. This not only helps in meeting customer demand but also ensures that manufacturing takes place on schedule. By optimizing material requirements and streamlining the control system, MRP systems play a crucial role in enhancing overall productivity and reducing manufacturing costs.
Master Production Schedule
The Master Production Schedule (MPS) is a critical component of material requirements planning. It is essentially a plan for future production, which includes both dependent and independent demand. The MPS lays out a detailed production schedule, taking into account sales forecasts, customer orders, and local inventory holding costs. The master schedule helps to ensure that the manufacturing process meets demand while minimizing inventory costs.
In the MPS, production and inventory management is optimized based on strategic inventory positioning. The master schedule serves as a bridge between the customer demands and the manufacturing process, aiding in the optimization of the production cycle and capacity planning.
MRP Systems
Material Requirements Planning Systems (MRP systems) are computer-based control systems that manage material requirements and schedule production activities. MRP systems process data from the master production schedule, bill of materials, and the inventory status file to generate detailed production schedules and purchase orders for raw materials.
Most MRP systems support functions beyond material planning. These include supply planning, operations management, and shop floor control. More comprehensive MRP systems, often called Manufacturing Resource Planning or MRP II systems, integrate additional modules such as sales order management, customer relationship management, and enterprise resource planning (ERP).
Benefits of MRP
The benefits of MRP are manifold, significantly enhancing the efficiency, flexibility, and profitability of manufacturing operations. By automating production planning and inventory management, MRP systems make factory workers more productive and improve product quality. They help manufacturers respond swiftly to increased customer demand, thereby avoiding production delays and inventory stockouts. Additionally, MRP systems eliminate manual processes, freeing up valuable time and resources. Businesses can plan and schedule production more efficiently, ensuring that customer orders are fulfilled on time. Moreover, MRP helps in reducing inventory levels and carrying costs by scheduling materials to arrive just in time for production, thus minimizing excess inventory and associated costs.
Limitations and Challenges of MRP
Despite its numerous advantages, MRP systems come with certain limitations and challenges. One of the primary challenges is the heavy reliance on accurate input data. Inaccurate data can lead to flawed production schedules, inventory shortages, and potential loss of contracts. Another significant limitation is the inflexibility in the production schedule, which can be problematic in dynamic manufacturing environments. Additionally, implementing MRP systems can be costly, and there is often a tendency to hold more inventory than necessary. Unlike comprehensive ERP systems, MRP may not account for production capacity, which can impact the availability of materials and overall production efficiency.
MRP vs. ERP
Enterprise Resource Planning (ERP) systems are an extension of MRP systems, offering a more comprehensive solution for managing all enterprise information. While MRP focuses on planning and controlling the resources within a company, ERP provides a single platform that integrates various business processes, including accounting, customer relationship management (CRM), manufacturing resource planning, and warehousing. ERP systems offer advanced functionalities in financial management, customer relationships, and sales order management, making them a holistic solution for enterprise-wide needs. MRP can function as a stand-alone application or as a component of an ERP system, addressing not just resource scheduling but the entire spectrum of business operations.
Manufacturing Resource Planning
Manufacturing Resource Planning (MRP II) is an extension of the original MRP system. MRP II integrates all the aspects of a manufacturing company into one complete system to control all resources associated with the manufacturing process. This type of planning system includes functions related to production planning, inventory management, and control system functions.
In addition to the features of traditional MRP systems, MRP II also incorporates modules related to capacity planning, master scheduling, and sales forecasts. Moreover, it interfaces with other management information systems such as the ERP system for more efficient and effective control of the entire manufacturing operation.
ERP software like those available from InvestGlass can provide comprehensive solutions, including functions related to sales, marketing, and automation, making them a crucial asset for modern manufacturing companies.
The successful implementation of an MRP or MRP II system can lead to improved manufacturing efficiency, reduced inventory costs, better utilization of resources, and increased customer satisfaction. However, to fully benefit from these systems, it is critical to maintain accurate data within the system. Data integrity is essential, as any errors in the bill of materials or the inventory status file can lead to production delays and excess inventory, defeating the purpose of materials requirement planning.
Implementing an MRP system or enhancing an existing one with MRP II features can transform a manufacturing operation, making it more responsive to customer needs, efficient, and profitable. To fully explore the potential of these systems, businesses should consider partnering with an experienced provider such as InvestGlass to ensure the system is well integrated into their operations.
Future of MRP
The future of MRP lies in its integration with cutting-edge technologies such as artificial intelligence (AI), machine learning (ML), and the Internet of Things (IoT). These technologies promise to enhance the accuracy and efficiency of MRP systems, enabling businesses to make more informed decisions and improve their supply chain management. The increasing adoption of cloud-based MRP systems is another trend, offering businesses greater flexibility and scalability. As the manufacturing industry continues to evolve, MRP will remain an essential tool for managing production inventory levels and the supply chain effectively, adapting to new technological advancements and market demands.
Conclusion
Material Requirements Planning (MRP) and Manufacturing Resource Planning (MRP II) are cornerstones of modern manufacturing operations. They streamline the planning process, manage inventory requirements, and boost scheduling production to meet demand. Leveraging these tools effectively can lead to significant improvements in manufacturing efficiency, inventory control, and customer satisfaction.
However, the successful implementation of these systems requires rigorous data management practices and staff training to ensure optimal use of the MRP software. With the help of partners like InvestGlass, businesses can harness the power of MRP and MRP II systems to adapt to changing market conditions, fulfill evolving customer needs, and turn potential challenges into opportunities for growth and success.